Surface preparation
Technological blasting to cleanliness grade Sa 2, degreasing, pressure washing, abrasive blasting to cleanliness grade Sa 2½ for coating application, roughness profile ISO comparator – Medium G.
Application of masses
Applied Products:
POLYGLASS PPA / PPV; CORROFILL VE; POLYGLASS VEF; LR 600+ QUADRAXIAL FABRIC 600 g/m²; POLYGLASS VEF WR
Applied coating systems:
NS-1A = 3 400 μm DFT; NS-1V = 3 400 μm DFT; NS-2 = 2 000 μm DFT
Applied substrate:
Inner surface of absorber; Carbon steel; 2 450 m² (lamination 1 450 m²)
Procedures:
- decontamination of visually unidentifiable impurities
- surface preparation according to ISO 8501-1 to purity grade Sa 2½
- POLYGLASS PPA / PPV primer application
- application of the POLYGLASS VEF corrosion barrier
- application of CORROFILL VE filler material
- application of laminating layer LR 600 + Glass cloth 600 g/m²
- application of the anti-abrasion layer POLYGLASS VEF WR
- carrying out the relevant quality tests according to the PKZ

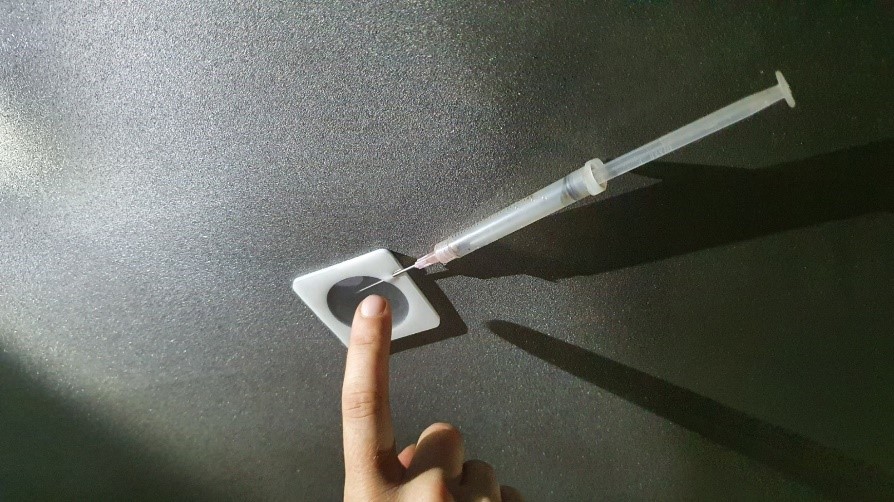
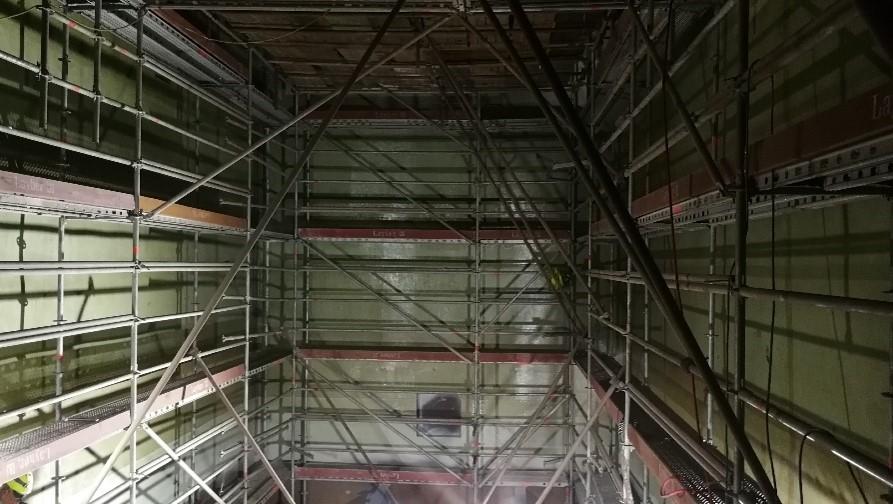
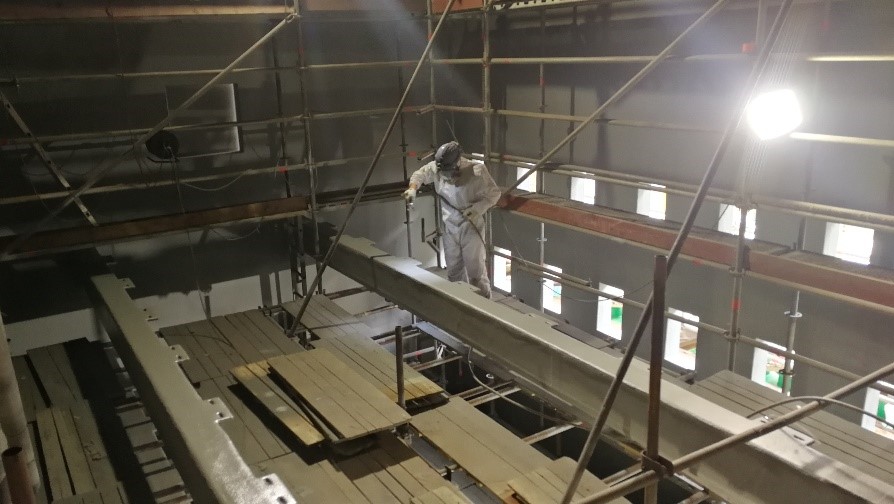
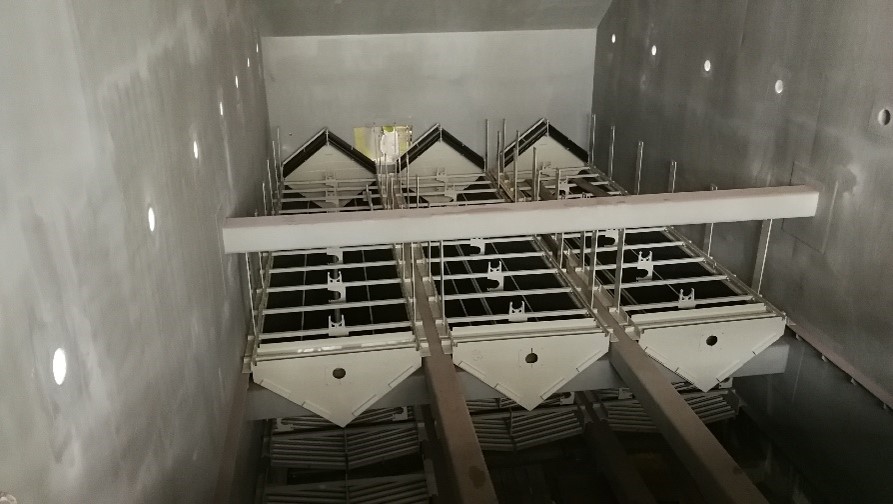
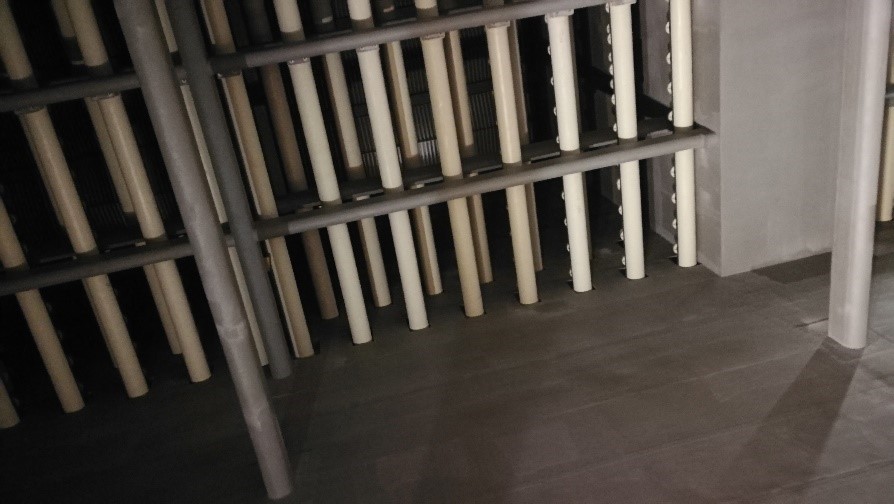
CORROTECH ENGINEERING s.r.o. provides highly professional services in the field of surface preparation and application of special coating systems for the most demanding stress environments and various industrial equipment. The CORROCOAT POLYGLASS VE vinyl ester coating system filled with special glass microflakes is the ideal choice for corrosion and abrasion protection of the internal parts of the flue gas desulphurisation absorber, protecting the substrate of the steel structure in the long term. The project was carried out directly for a foreign technology supplier in the full coverage of the internal parts of the absorber building, covering 2,450 m² (of which 1,450 m² with the application of lamination reinforcement) in critical parts of the structure with high temperature operation and full immersion. In the process of abrasive blasting with steel grit, a mobile suction and recycling unit from MAL MECHATRONIK was used with a positive impact on the speed of the process and minimal requirements for hazardous waste disposal.
CORROCOAT has been successfully fighting corrosion for more than 45 years. It uses innovative mechanical engineering combined with anti-corrosion technology to provide long-term protection for both new and damaged equipment. It uses special composite and structural coatings in conjunction with technical processes to individually address corrosion problems. With a focus on quality, refurbishment procedures are a proven, cost-effective weapon to win the battle against corrosion in the long term.